LOCATION:
SYSPRO Introduction
> MANUFACTURING
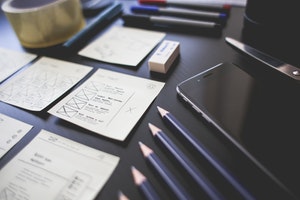
Bill of Materials
SYSPRO Bill of Material (BOM) is designed to ensure your organisation has complete control over the product structure. This module ensures that engineering, production, purchasing and order processing are utilizing the same information. The Bill of Materials is defined by the manufacturing process and includes: work centers, labor, tools, dies, inserts, fixtures, raw materials, packaging, scrap rates, setup times, yields and equipment.
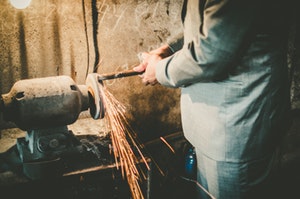
Work in Progress
SYSPRO Work in Process module is the cornerstone of the system’s Manufacturing Solution. It allows you to issue work orders, develop schedules, and track costs associated with the manufacturing process. Work in Process module provides you with complete control of the manufacturing process and the ability to see up-to-the-minute, work-in-process information.
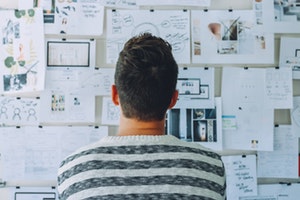
Requirements Planning
SYSPRO Requirements Planning assists you in managing the balance between supply and demand. The Requirements Planning module uses projected and actual demand and supply to assist in planning and creating realistic production, purchasing and supply transfer schedules. It also identifies capacity constraints and maintains optimal stock holdings in a multi-site and multi-warehouse environment.
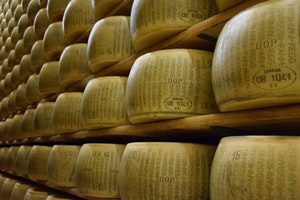
Lot Traceability
SYSPRO Lot Traceability is designed for manufacturers that require controls over product tracking to achieve compliance and also to maintain quality and reputations. Within industries, such as aerospace, automotive, consumer packaged goods, medical device, pharmaceutical, food and beverage and numerous others, it has become increasingly important to be able to locate specific lots of finished goods to speed recalls when a defect or hazard of a particular part or ingredient has been identified.
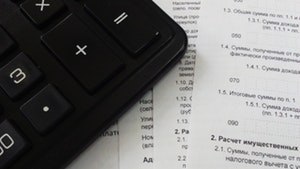
Activity Based Costing
SYSPRO software facilitates calculations that assist in determining product profitability. Certain overhead costs which are typically accumulated against items by attaching elements of cost at the transition points of purchasing, manufacturing or selling, often comprise a significant portion of the total cost of a product and can impact profitability.
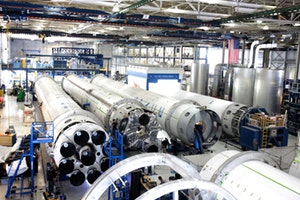
Engineering Change Control
Manufacturers need the ability to bridge the gap between engineering, quality assurance, and production to control and speed the process of driving new product revisions to market quickly and cost-effectively.SYSPRO Engineering Change Control (ECC) module enforces controls in product design with a user-defined workflow that can supplement or replace the paper trail that usually accompanies any product design or changes to product design.
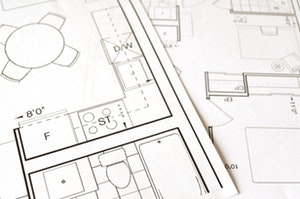
Factory Documentation
SYSPRO Factory Documentation facilitates clear and accurate user-defined shop floor documentation for production operations to be performed and materials to be issued, thereby enabling accuracy and efficient control of production processes.
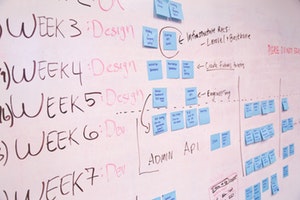
Factory Scheduling
SYSPRO Factory Scheduling (SFS) provides the capability to schedule production to a detailed level considering the capacity constraints in the production environment. SFS applications range from the simple Graphical Planning Board to the very sophisticated Advanced Scheduler, with the latter classified as an Advanced Planning and Scheduling (APS) system.
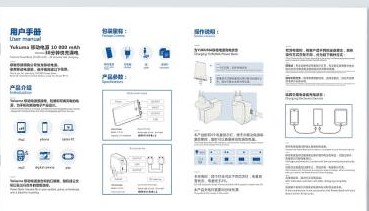
Product Configurator
There are many business benefits to be gained by using SYSPRO’s Product Configurator to replace manual processes. This allows companies to work smarter and eliminate the wasted effort when tracking orders, quotes, jobs, and more.
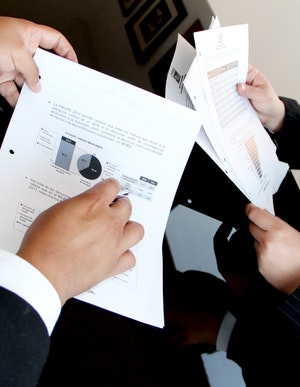
Quotations
SYSPRO’s Quoting and Estimating capabilities allow you to create professional and comprehensive quotations. A highly flexible interface provides you with all the information you need to give your customers timely quotes/estimates. The Quotations and Estimates allow for the creation of a quote/estimate for either an existing customer or prospect or for either an existing inventory item or a non-inventory item.
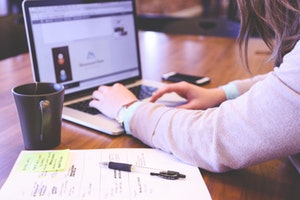
Projects and Contracts
The Projects and Contracts system caters for progress billings, deposits and retentions. You can define schedules against which progress billings must take place and the method of billings.